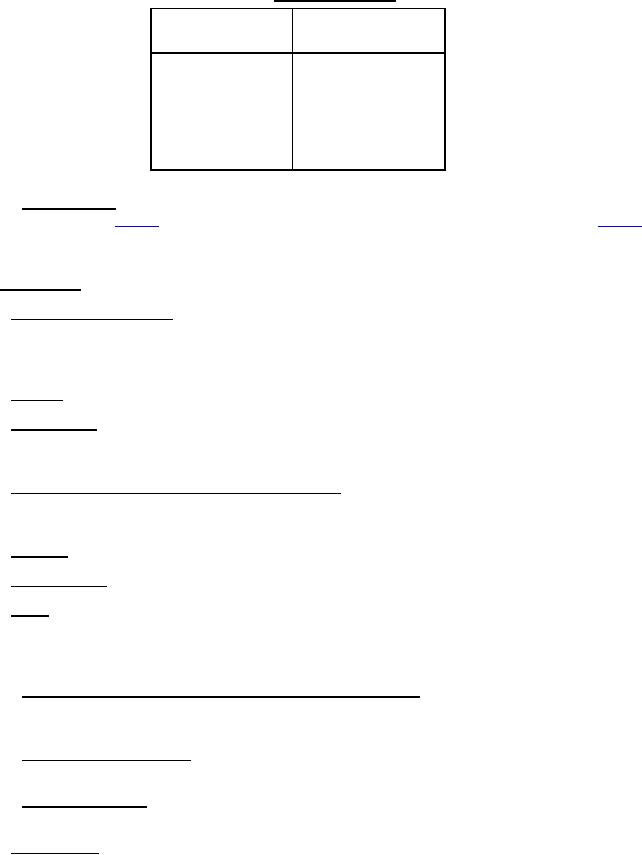
MIL-PRF-19769C(NAVY)
TABLE III. Sampling procedure.
Number of Gaskets
Number of Gaskets
in Lot
to be Selected
1 to 25
All
26 to 50
22
51 to 100
27
101 to 400
33
Over 400
36
4.3.2.3 Rejection of lot. Each of the samples selected in accordance with 4.3.2.2 shall be subjected to the lot
acceptance examinations in table II. If any gaskets do not conform to the requirements for lot acceptance in table II,
the lot which the gaskets represent shall be rejected. Rejected lots may be submitted for reinspection only after all
gaskets are reexamined and all defective gaskets are removed.
4.4 Test methods.
4.4.1 Dimensions and tolerances. Each gasket shall be inspected to ensure that dimension and tolerance
requirements are met. All dimensions shall be measured with an instrument capable of measuring to at least one
decimal place more than the specified tolerance or, if no tolerance is specified, at least one decimal place more than
the specified dimension.
4.4.2 Marking. Each gasket shall be inspected to ensure that gasket marking requirements are met (see 3.7).
4.4.3 Workmanship. Each gasket shall be visually inspected to ensure that gasket workmanship requirements
are met. Minor surface defects, including minor defects specified in MIL-STD-407, that do not affect the
serviceability of the material shall not be cause for rejection.
4.4.4 Tensile strength, tensile stress, and ultimate elongation. Tensile strength, tensile stress at 100 percent
elongation, and ultimate elongation shall be determined in accordance with ASTM D412, Test Method A, with
Die C test specimens.
4.4.5 Hardness. Hardness shall be determined in accordance with ASTM D2240, Type A durometer.
4.4.6 Specific gravity. Specific gravity shall be determined in accordance with ASTM D792.
4.4.7 Aging. Specimens for tensile strength, tensile stress, ultimate elongation, hardness, and compression set
tests following aging shall be aged in a circulating air oven at a temperature of 194±2 °F (90±1.1 °C) for 46 hours.
The aged samples shall be tested not less than 20 hours nor more than 48 hours after removal from the oven. After
4.4.7.1 Tensile strength, tensile stress, and ultimate elongation after aging. Tensile strength, tensile stress, and
ultimate elongation shall be determined in accordance with 4.4.4 after the tensile specimens have been aged in
accordance with 4.4.7.
4.4.7.2 Compression set after aging. Three specimens shall be tested in accordance with ASTM D395, Test
Method B, using a 25 percent deflection after being aged in accordance with 4.4.7.
4.4.7.3 Hardness after aging. Hardness shall be determined in accordance with 4.4.5 after the hardness
specimens have been aged in accordance with 4.4.7.
4.4.8 Oil immersion. Specimens for swell, tensile strength, tensile stress, and ultimate elongation tests
following oil immersion shall be immersed for 94 hours at 158±3.6 °F in a petroleum-base oil having the same
viscosity, aniline point, and flash point as the No. 3 oil of Method 6001 of FED-STD-601. After oil immersion,
6
For Parts Inquires call Parts Hangar, Inc (727) 493-0744
© Copyright 2015 Integrated Publishing, Inc.
A Service Disabled Veteran Owned Small Business