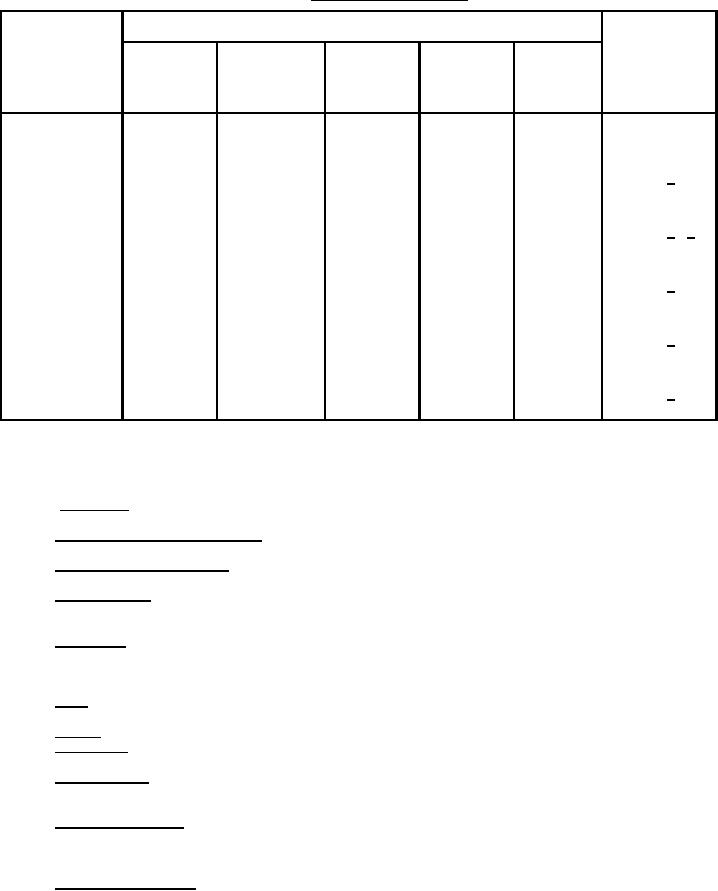
MIL-PRF-24790A (SH)
TABLE IX. Packing substitution table.
PUMP PARAMETERS
Max differ.
Asbestos-
Max
pressure
Non-Asbestos
containing
Rod speed
across packing Max system
substitute
specification
(fpm)
(psid)
temp (ºF)
Medium
Type
packing
MIL-P-17303
Class I, Type B
4000
150
250
Fresh water
Rotary
Type I,
or C
Class A (2/)
170
300
420
Sat. L.P.
Recip.
Type II,
Class I, Type D
steam
Class A (1/, 2/)
4000
150
250
Fresh water
Rotary
Type I,
MIL-P-24377
Class A (2/)
Type I,
1700
625
75
Seawater
Rotary
Class A (2/)
Type I,
5400
100
300
Boiler
Rotary
Class A (2/)
feedwater
1/ For use in steam applications only.
2/ Not to be used in pumps where the packing runs directly against a shaft or shaft sleeve made of 400 series
stainless steel and where the shaft or sleeve is not clad with a different material.
6.6 Definitions.
(a)
Average overall shaft temperature. The sum of all temperature readings during the thermal cycle period,
divided by the total number of temperature readings during the thermal cycle period.
(b)
Average overall leakage rate. The sum of all leakage rate readings divided by the total number of leakage
rate readings.
(c)
Break-in period. A 30-hour period prior to the start of actual testing, during which leakage rate is
gradually decreased from an initial free leakage rate, with the objective of reaching average overall
leakage rate by the end of the period.
(d)
Normal run. A 480-hour test period for Type I, Class A packings, during which the test fixture is
operated at rated temperature and pressure. During the 480-hour run, fixtures are stopped and cooled
down from operating temperature to ambient temperature a minimum of four times. The cooling-down
periods are separated by intervals of at least 8 hours.
(e)
PSID. Pounds per Square Inch Differential. This is the pressure capability of a packing expressed as the
maximum differential pressure across the packing.
(f)
Sample. A spool or reel of packing selected for qualification or quality conformance testing.
(g)
Sample size. The number of spools or reels to be randomly selected from completed lots of spools or reels
for qualification or quality conformance testing.
(h)
Size of packing. The cross-sectional distance between parallel faces, for square and trapezoidal packings.
In the case of rectangular packing, it is the distance between the longest parallel faces; for round or oval
packing, it denotes the maximum diameter.
(i)
Thermal cycle period. The normal run period, or the period which commences at the end of the break-in,
and which extends to the start of the temperature transient period, in the case of low-speed Type I, Class
A packing tests. For Type II, Class A packing tests, the thermal cycle is the 336-hour period which
follows the break-in, during which the test fixture has alternate hot-run and cool-down times.
(j)
Uncontrollable leakage. That condition when continued tightening of the packing gland has no effect on
lowering the packing gland leakage rate.
11
For Parts Inquires call Parts Hangar, Inc (727) 493-0744
© Copyright 2015 Integrated Publishing, Inc.
A Service Disabled Veteran Owned Small Business